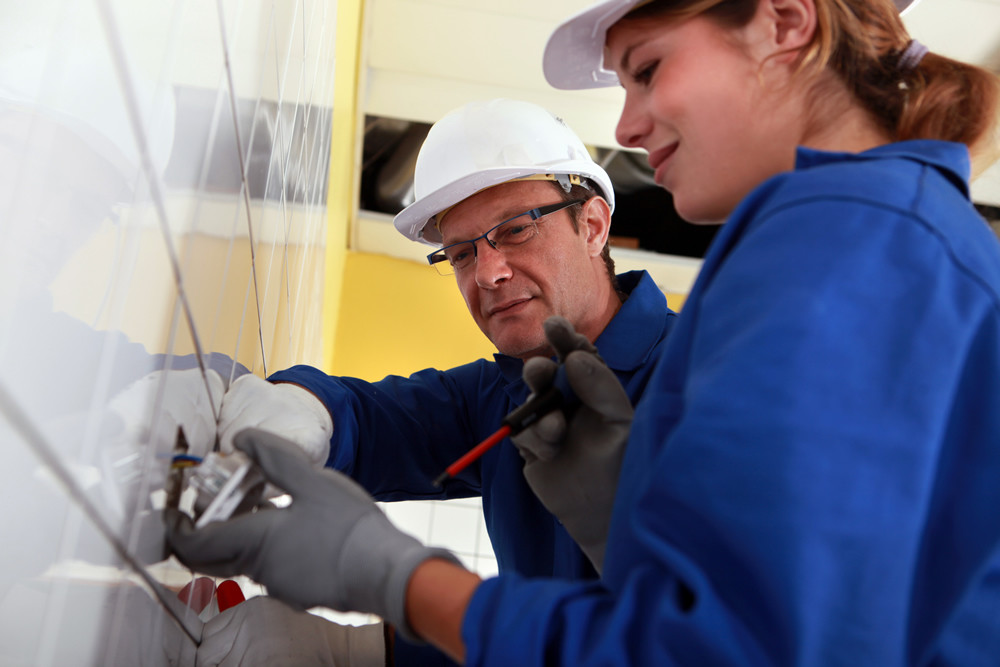
Challenge:
When a catastrophic flood/cloud burst/heavy rain occurs, millions of rupees of equipment is drenched and covered and possibly filled with all kinds of dirt and muck. Some may be replaced with insurance covering the tab, but much of the equipment will need to be repaired and brought back into service as soon as possible.
Believe it or not many electronic and electrical components can handle exposure to water, and it is actually a common way to clean assemblies in manufacturing processes. Some components, like power supplies, can’t be recovered, but much of it can. Before you start, remember these imperative tips:
- Electrical and Electronic devices should be disconnected from power and all batteries removed until everything is clean and 100% dry. Connecting power too soon could cause short circuiting, which would be destructive to the device and potentially dangerous to you. Be patient!
- With sensitive electronics, it is important to avoid static build-up. Ideally use a grounding strap, or at least discharge frequently by touching a grounded metal surface away from your work.
Step 1: Rinse Equipment with Clean Water
Electronic and electrical equipment should be flushed well with clean water to remove salt, sediment and particulate matter. Disassemble the equipment to allow access to all interior parts and flush with water until the rinse water is clean. If possible, dip the equipment into a drum or tank of clean water and agitate to dislodge trapped contaminants.
Spray components with MRO 1023 H2O DISPLAZER which has the benefit of being hydrophobic, so it repels moisture and carries it away from the parts. To speed the drying process, use MRO 1002 OFFLINE KLEANER to blast away moisture and solvent, even out of tight crevices. After the equipment has been rinsed thoroughly, stand it on end and allow it to drain.
Step 2: Remove Remaining Oil, Grease, Sludge and Other Contaminants
It’s important to remove all oxidized oil, grease and other contamination. Most contacts and connectors contain sensitive plastics that will be destroyed using heavy degreasing solvents including MRO 1003 Safety Sol. For plastic-safe precision cleaning, use MRO 1002 OFFLINE KLEANER, or for heavy-duty nonflammable degreasing use MRO 1004 ELECTRIK MOTOR KLEANER/MRO 2006 NON CHLORINATED KLEANER(Bulk). MRO INFRA aerosol cleaners feature a powerful spray force that helps dislodge any remaining trapped contaminants. Spray the equipment thoroughly or dip the equipment in the solvent and agitate while submerged.
Where removal of caked on grease, sludge and other contamination is required, a brush can be used for the most stubborn soils. Use brushes made of natural fibers, which tend to be less abusive to sensitive surfaces and components, and less likely to generate static synthetic bristles. Metal bristles should be avoided except for removing oxidation from contacts in the most extreme cases.
When wiping is required, whether for extra scrubbing action or soaking up excess water and solvent, lint-free poly cellulose material is recommended. These wipes are made of a combination of polyester and cellulose fibers, giving them both absorbency and strength. Paper towels will tend to shred and shop towels can produce too much lint for delicate equipment.
Make sure that all contaminated areas have been sprayed and completely cleaned. Allow the equipment and assemblies to drain and dry completely before returning them to service.
Step 3: Test Equipment
Test electrical equipment to ensure correct resistance levels have been achieved prior to operating equipment. If correct levels have not been reached, then it may be necessary to repeat Step 2 of this procedure. When correct resistance levels have been reached, energize equipment under “no-load” conditions and allow operating for a period of time before returning to normal operations.