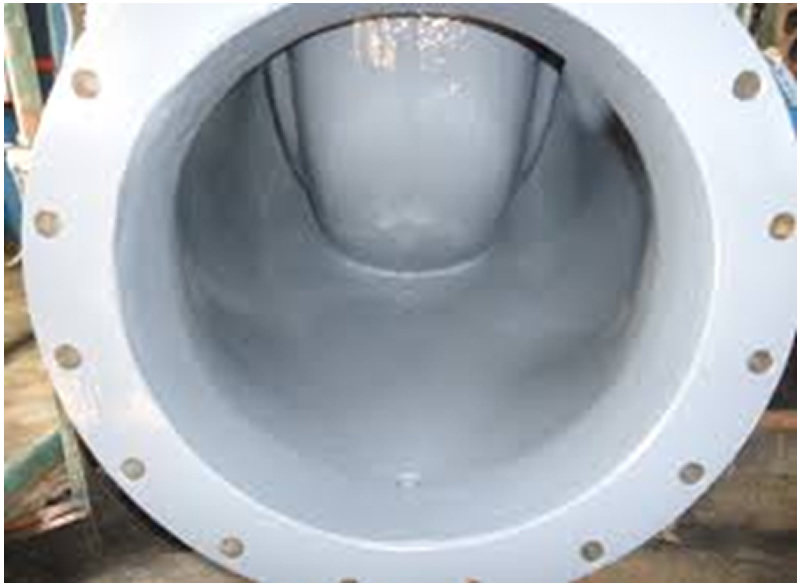
The Challenge
After prolonged usage, certain areas of the pump were suffering from cavitations damage, which in turn was hindering the efficiency of the pumping system.
The Solution
MRO 1011 Kleaner Degreezer
MRO 8000 Ti Putty
MRO 3003 Brushable Ceramic
MRO 3004 Super Glide
APPLICATION METHOD
Firstly, all machined faces were protected from the blasting process. Then shot blast upper and lower casings to SA 2 ½ and produce a surface profile of no less than 75µm. The application area was then vacuumed and examined to make sure it was dust free and all the blast media was removed. Finally the area to be coated was cleaned with MRO 1011 Kleaner Degreezer.
Once the substrate had been tested to be free from salt contamination, the area to be repaired was then marked for application of MRO 8000 Ti Putty to rebuild the areas of undulation and pitting damage. After MRO 8000 Ti Putty had cured and within the two-hour coating window, the first coat of MRO 3003 Brushable Ceramic was applied. This was followed by the coat of MRO 3004 Super Glide to achieve a total dry film coating thickness of 400 microns.

The Result
WHY MRO 6004 TRANSFORMER MAINT KIT?
This coating would provide long-term erosion and corrosion protection to the equipment and improve the efficiency of the pump. In fact, MRO 3004 Super Glide has been seen to increase efficiency by up to 3% on new equipment and up to 15% on refurbished equipment.
APPLICATION CASE HISTORY – A CHEMICAL PLANT IN VADODARA, GUJARAT
Drop in efficiency of pump due to cavitations damage.
CUSTOMERS BENEFIT:
MRO INFRA coating provided long-term erosion and corrosion protection to the pump and improved the efficiency of the pump by 7 %.